Lifting your 2WD astro/safari
Posted: Tue Sep 19, 2006 1:55 pm
Installation of 5” lift kit on 95 RWD Chevy Astro Contributed By BLAZER
The following description is of the removal of the stock suspension and the installation of a 5” lift kit which is composed of heavy duty 3” front lift springs, 2” body blocks, 3” rear lift shackle, 2” axle blocks, and new shocks. I used some parts I received from Overlandvans.com, Summit Racing, and some I had, but I recommend buying the complete kit from Overland vans to simplify things.
The instructions will be broken down into three sections, body lift, front springs, and the rear lift.
This install was completed on a 95 Astro RWD, but the body lift and front spring install will also blanket 85-2005 astro/safaris, the rear spring lift will blanket 95&up vans with the leaf springs.
Installation of 2” body blocks:
1. Always make safety first, make sure rear tires are blocked, engaging emergency brake is a good idea.
2. Start by removing/loosening following pieces….
A. Remove upper section of fan shroud. Some people say to trim bottom of shroud, but I will explain how to use spacers in later step. Remove 3 bolts across front radiator support and the 4 bolts on the middle of shroud. With some persuasion, the upper section can be lifted up and out of van ( air cleaner assembly will need to be removed)
B. Make sure shifter is in park and loosen bolt clamp on the shifter linkage. This will be re-adjusted in later step.
C. Remove grill, 4 bolts across the top, couple bolts in the middle and bottom pops off.
D. Remove front bumper cover, 4 bolts in center, 4 bolts under front fender, and the two support brackets holding this on, lay cover to side for later install.
E. Remove the emergency brake cable bracket from under body (near tranny cross member) save bolts for later.
3. You will now proceed in installing the lift body blocks ( hockey pucks) by first loosening all the
Body bolts, but leaving them in place (front/rear take 18mm, center takes 21mm).
4. Now you can remove all bolts on one side of van while other side is lose. Use a floor jack with a
long 2x4 under the body under door area and carefully jack up van off of the stock body bushing and continue until there is enough room to slide the new 2” blocks in between bushings and body. Start the bolts up through blocks and into body, leaving them lose for now, just get them started.
Note: the center blocks use larger diameter bolts and have larger holes.
The front may prevent a problem in alignment until other side is in place and level, then you can go back and re-jack up the first side and get it realigned. (Note, this is my install method, I have talked to people who have done front to back which may allow for easier alignment. Just make sure at least some bolts are left in as not to lose the alignment of the sub frame with the body.)
Once all body blocks are in place and all bolts are started, you can tighten them all down to factory specs. (I personally just tighten them to basically as tight as I could).
5. Once the blocks are in place, you can now adjust the shifter lever. With the bolt being lose, push
The rod up and then tighten the clamp bolt. This should put the shifter in the correct position. If not, you may have to loosen and check the shifter indicator on the dash and then adjust and re-tighten.
6. Next is to re-install the emergency brake bracket. You can get a new bracket from Overland vans, but I modified mine to work. First jack up the transmission at tail shaft and loosen center mount nut. Then remove the 4 bolts holding the cross member in place. This will allow for you to slide the e-brake cable up and over the cross member and remove some stress on the cable the blocks created. Once the cable is on top, the cross member and tranny can all be replaced and tightened. Now the cable must be stretched and slide out of the slip joint. Once that is done, squeeze the three metal prongs together on the bracket and remove bracket form cable. Drill a hole same size as bottom hole 1 ¾” up and then re-install bracket on cable, cable in slip joint and then bolt bracket back to body. Check to make sure e-brake functions properly. If new brackets were bought from Overlands, follow their directions.
7. The fan shroud will now be modified using some 2 ½ bolts with nuts and some 2” spacers. I used some steel water/gas pipe and cut them to 2”, PVC water line may also work, just make sure the pipe is just big enough to fit over bolts. There will be 4 speed clip s in the bottom section which needs removed so the bolts will go through holes. Carefully place bolts through holes, while also placing flat washers on both top and bottom of spacers. This prevents spacers from pushing through plastic. Then tighten nuts on bolts and the shroud will know have a two inch space between upper/lower section. This may take two people, preferably with small hands to place nuts on bolts and holding everything all together. Lower shroud sits lower and out of its hold down slots, but I have had no problems with rub or it hanging loose. The air intake box may now sit higher and the hose may not line up correctly. I had and aftermarket K&N air intake so I just re-adjusted mine.
8. Final step is to replace the front bumper cover. The main bracket in front is basically raised to next hole and bolt placed on each side. I made a 1 ½”x 8” flat bracket and drill three holes in it which aligned with to hole in bumper bracket and lower hole in frame. Not sure how much better it will work, but at least it will give some support for the bumper. If new bumper brackets were bought from Overlands, follow their directions.
Installation of Overland’s front 3” Heavy duty lift coil springs:
1. If tires and e-brake are not sill used from body lift, make sure rear tires are blocked and e-brake is
Engaged.
2. Begin by jacking up and removing front tires (I did one side at a time). After tires are removed,
Place jack stands under sub frame under the door section. I also kept a floor jack under the center cross member for safety.
3. You will need to remove the brake caliper and wire them up and out of the way. Make sure they just don’t hang, that can damage the hoses.
4. You can now being to take things apart. First order of business is to remove old shocks. You can get to the top bolt by pushing wheel well flap back, but it was easier to remove nut from upper ball joint ( this has to come lose anyway) and push upper control arm up and back . The ABS cable will have to be removed from its clips that run along the top of the arm. Get a drill and drill out the rivets. If done properly, the clips will stay on the arm and the cable will be able to be put back in them on reassembly. Remove cotter pin, then loosen the nut, but leave on by a few threads. Them take a hammer and hit the spindle housing where the ball joint goes through. After a few whacks, the arm should pop up and you can finish removing nut. Once you have the upper arm lose, you can see the top shock bolt/nut. There is a special tool that makes this removal easier, but an open end wrench and vise grips can work also. I ended up using a 4 ½” angle grinder with a metal cutoff blade and cut the nut/bolt off. Just be careful not to cut into the arm or frame area. Once you get that lose, you can remove the lower bolts form the lower arm, 13mm socket will do the trick. Once that is lose, you can wiggle the shock down and out. Keep the lower bolts; you will need for new shocks.
5. Now the stabilizer bar needs disconnected. This will take a wrench and socket. All that needs to be done is the nut removed and the bushings taken off. This will allow the bar to be free. This would also be a good time to install need links while our in there if so desired.
6. Next, the old stock spring will need to come out. Since the upper arm is already apart, this is just a matter of pushing the lower control arm and spindle/brake rotor down and getting spring out. This may take some persuasion with a crowbar, mine actually came out fairly easy. Once this is out, you can clean all the dirt buildup from the spring pockets. Now on to the most fun part……
7. Install of new lift springs…these are some bad boys!!!! I Express EXTREME CAUTION at this step, these springs need to be compressed and are very dangerous. These springs have to compressed some to get them in. I rented and inside spring compressor from Autozone and compressed my springs with an air hammer. Be very careful with these as there is a lot of compressed energy just waiting to get lose and hurt someone. Once these are compressed they can be installed into the spring pockets. There is only one way to install, the flat goes to the top, the open coil goes on bottom with the end of the coil being placed between the two small holes in the spring pocket, this gives proper alignment. The stock springs came with a rubber isolator on top, I tried to re-install, but they wouldn’t stay on so I left them off, no problems since. This was the worst step of the entire lift to try to get spring in the pocket and back in. I ended up placing a small jack under the control arm and putting some pressure on it while trying to pry spring into the pocket. This took some finesse and a lot of prying and jacking, I still don’t know I got them in, but I did. The last one actually had the spring compressor let lose just as it slipped into place…..That’s what I meant by extreme caution, I could have had a broken leg or something if it would have come out instead of in. I would recommend having a professional install these for you if you have any reservations about this step. Once they are in and seated, you can begin putting everything back together in reverse order. I also recommend before reconnecting the upper arm, remove the upper rubber bump stop from the arm and cut it down some. I used two screwdrivers to pry it out from the top and then took it to the bench and used a cut off tool in my angle grinder cut approx ½- ¾” off of it. Cutting of the bump stop allows the top control arm to come down enough to get ball joint back into hole and re-attached. Then I replaced and continued with replacement of all parts in reverse order; upper control arm/ball joint, stabilizer bar, brakes, ABS cable, shocks, and then tires. Make sure everything is tight and steering works correctly.
Installation of 2” rear axle blocks, rear add a leaf, and shocks:
1. As in the other steps, make sure vehicle is in park and front wheels blocked. Jack up rear of van, remove rear tires, and place jack stand under rear frame right in front of rear springs. I left jack under differential and placed another jack stand under my trailer receiver for extra safety (if you have one).
2. Begin by removing the rear shocks, saving both the top and lower bolts and nuts as they will be re-used on the new shocks; discard old shocks will be needed with lift.
3. Now begin removing Ubolts and bolt/nut assemblies that hold axle to leaf springs. The jack under the axle will be need to lower the axle once lose from springs. Once the bolts are off, you can then lower axle and proceed to either placement of either axle block or extra leaf.
A. The rear axle lift block can be purchased at your local auto shop or through Overlands. I used a 2” block and had to get new ½” Ubolts as the supplied ones were too long for my astro. Once the old Ubolts are lose, you can lower jack and separate the axle from springs. I removed the rubber pad and placed the new block in between the axle and springs. The center hole may need enlarged slightly to fit over the leaf spring center pin. Once in place, raise jack and get axle/block back in place. Then the new Ubolts can be put in place and finger tighten on top plate. The inner bolts will need replaced as they will now be too short. Place the lower bracket on a work bench or place in vise and pound out the old bolts. The are tack welded in place so some force may be required. Once they are out, replace with some new grade 8, 3” bolts. I also bought some ½” black iron pipe and cut to 2” to use as a spacer between the upper and lower brackets. Once you get all the assembly together, you can then tighten all bolts to specs (I just torqued everything down pretty tight).
B. The other choice is using Overland’s add a leaf (use their instructions if included) which also requires the Ubolt/inner bolts to be remove and the axle to be separated from axle. The spring retaining clamps on each end must then be bend open so springs can be separated; this can be done with crowbar/large pry bar. After that is done, the center pin can be removed to allow the separation of springs either by unbolting or using cut off tool. Place a large C clamp on spring near center to prevent spring from flying apart once center pin is removed. Slowly remove clamp to allow springs to separate. Now place the add a leaf spring in its proper place (follow Overlands instruction). NOTE: I used a leaf spring out of a K5 blazer as my add a leaf. I had to cut the ends down some and it was just slightly wider, but worked fine and I placed it directly under the top spring. This gave me about an inch extra lift and slightly more carrying capacity.
Once you get your leaf in place, use the c clamp to compress the pac so you can put the new longer center pin back in. Once that is in and tight, replace the Ubolts/inner bolts and bracket and tighten everything back up. You then will need a large c clamp (6”) to squeeze the spring retaining clips back together.
4. Now that you have either your blocks in or leafs, the new shocks can be installed. I chose the recommended Rancho shocks form Overlands’ website. There will be supplied steel bushing which need to be place inside the poly bushings in the shocks. You can then replaced the factory bolts/nuts and tighten. These need to be fairly tight or you will get a banging noise when hitting bumps, but not too tight as to crush the poly bushing. If you do get a banging after install, just retighten nuts. Replace the wheels and you should be ready to go.
Hopefully, these instructions will cover the complete install of the lift kit on a rear wheel drive astro/safari.
Remember after install it is important to have van properly aligned at a tires store. I had problems with too much positive camber and my alignment guy recommended I order some offset upper control arm inner shafts to correct. He stated he could place shims in there to get proper alignment, but he was afraid that it would make van too unsafe to drive. As of this writing, shafts are ordered and will be installed. I also recommend after a week or two of driving to go back over every nut/bolt and check tightness as things may work lose as they settle in.
09/20/06: UPDATE, upper offset control arm shafts were installed and alignment was set perfect, they were definitely the trick I needed.
Marty Sackenheim
“BLAZER”
Contact at;
http://www.astrosafari.animegrafx.com
blazercdr@yahoo.com
2wd Astro w/5" Lift
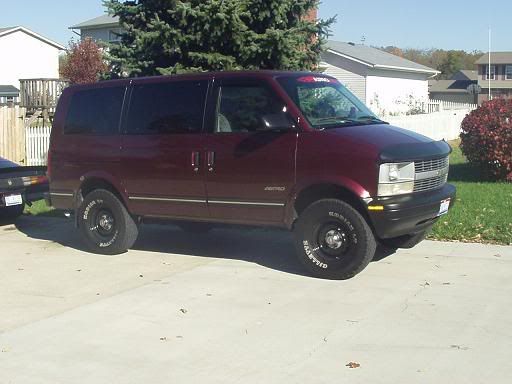
Front body Lift
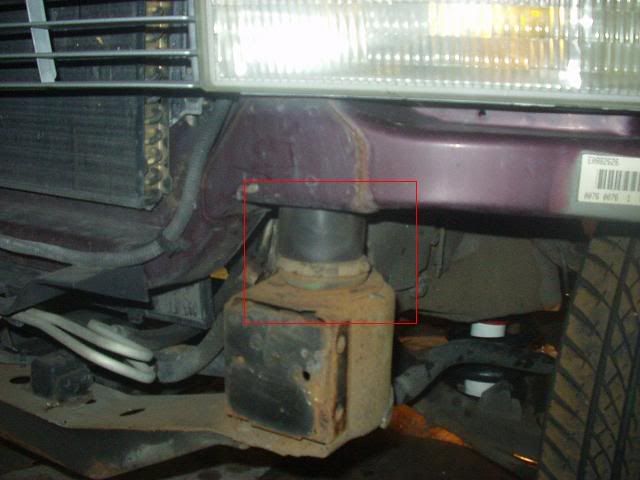
Rear Shackles
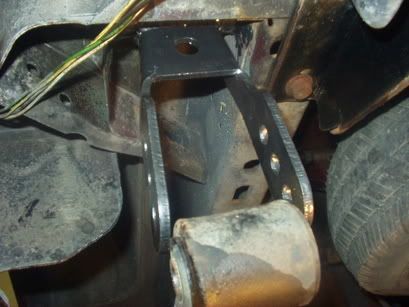
Coils (new and old)
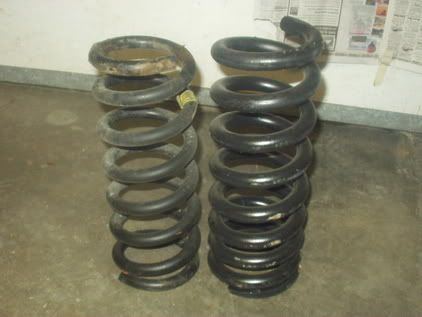
The following description is of the removal of the stock suspension and the installation of a 5” lift kit which is composed of heavy duty 3” front lift springs, 2” body blocks, 3” rear lift shackle, 2” axle blocks, and new shocks. I used some parts I received from Overlandvans.com, Summit Racing, and some I had, but I recommend buying the complete kit from Overland vans to simplify things.
The instructions will be broken down into three sections, body lift, front springs, and the rear lift.
This install was completed on a 95 Astro RWD, but the body lift and front spring install will also blanket 85-2005 astro/safaris, the rear spring lift will blanket 95&up vans with the leaf springs.
Installation of 2” body blocks:
1. Always make safety first, make sure rear tires are blocked, engaging emergency brake is a good idea.
2. Start by removing/loosening following pieces….
A. Remove upper section of fan shroud. Some people say to trim bottom of shroud, but I will explain how to use spacers in later step. Remove 3 bolts across front radiator support and the 4 bolts on the middle of shroud. With some persuasion, the upper section can be lifted up and out of van ( air cleaner assembly will need to be removed)
B. Make sure shifter is in park and loosen bolt clamp on the shifter linkage. This will be re-adjusted in later step.
C. Remove grill, 4 bolts across the top, couple bolts in the middle and bottom pops off.
D. Remove front bumper cover, 4 bolts in center, 4 bolts under front fender, and the two support brackets holding this on, lay cover to side for later install.
E. Remove the emergency brake cable bracket from under body (near tranny cross member) save bolts for later.
3. You will now proceed in installing the lift body blocks ( hockey pucks) by first loosening all the
Body bolts, but leaving them in place (front/rear take 18mm, center takes 21mm).
4. Now you can remove all bolts on one side of van while other side is lose. Use a floor jack with a
long 2x4 under the body under door area and carefully jack up van off of the stock body bushing and continue until there is enough room to slide the new 2” blocks in between bushings and body. Start the bolts up through blocks and into body, leaving them lose for now, just get them started.
Note: the center blocks use larger diameter bolts and have larger holes.
The front may prevent a problem in alignment until other side is in place and level, then you can go back and re-jack up the first side and get it realigned. (Note, this is my install method, I have talked to people who have done front to back which may allow for easier alignment. Just make sure at least some bolts are left in as not to lose the alignment of the sub frame with the body.)
Once all body blocks are in place and all bolts are started, you can tighten them all down to factory specs. (I personally just tighten them to basically as tight as I could).
5. Once the blocks are in place, you can now adjust the shifter lever. With the bolt being lose, push
The rod up and then tighten the clamp bolt. This should put the shifter in the correct position. If not, you may have to loosen and check the shifter indicator on the dash and then adjust and re-tighten.
6. Next is to re-install the emergency brake bracket. You can get a new bracket from Overland vans, but I modified mine to work. First jack up the transmission at tail shaft and loosen center mount nut. Then remove the 4 bolts holding the cross member in place. This will allow for you to slide the e-brake cable up and over the cross member and remove some stress on the cable the blocks created. Once the cable is on top, the cross member and tranny can all be replaced and tightened. Now the cable must be stretched and slide out of the slip joint. Once that is done, squeeze the three metal prongs together on the bracket and remove bracket form cable. Drill a hole same size as bottom hole 1 ¾” up and then re-install bracket on cable, cable in slip joint and then bolt bracket back to body. Check to make sure e-brake functions properly. If new brackets were bought from Overlands, follow their directions.
7. The fan shroud will now be modified using some 2 ½ bolts with nuts and some 2” spacers. I used some steel water/gas pipe and cut them to 2”, PVC water line may also work, just make sure the pipe is just big enough to fit over bolts. There will be 4 speed clip s in the bottom section which needs removed so the bolts will go through holes. Carefully place bolts through holes, while also placing flat washers on both top and bottom of spacers. This prevents spacers from pushing through plastic. Then tighten nuts on bolts and the shroud will know have a two inch space between upper/lower section. This may take two people, preferably with small hands to place nuts on bolts and holding everything all together. Lower shroud sits lower and out of its hold down slots, but I have had no problems with rub or it hanging loose. The air intake box may now sit higher and the hose may not line up correctly. I had and aftermarket K&N air intake so I just re-adjusted mine.
8. Final step is to replace the front bumper cover. The main bracket in front is basically raised to next hole and bolt placed on each side. I made a 1 ½”x 8” flat bracket and drill three holes in it which aligned with to hole in bumper bracket and lower hole in frame. Not sure how much better it will work, but at least it will give some support for the bumper. If new bumper brackets were bought from Overlands, follow their directions.
Installation of Overland’s front 3” Heavy duty lift coil springs:
1. If tires and e-brake are not sill used from body lift, make sure rear tires are blocked and e-brake is
Engaged.
2. Begin by jacking up and removing front tires (I did one side at a time). After tires are removed,
Place jack stands under sub frame under the door section. I also kept a floor jack under the center cross member for safety.
3. You will need to remove the brake caliper and wire them up and out of the way. Make sure they just don’t hang, that can damage the hoses.
4. You can now being to take things apart. First order of business is to remove old shocks. You can get to the top bolt by pushing wheel well flap back, but it was easier to remove nut from upper ball joint ( this has to come lose anyway) and push upper control arm up and back . The ABS cable will have to be removed from its clips that run along the top of the arm. Get a drill and drill out the rivets. If done properly, the clips will stay on the arm and the cable will be able to be put back in them on reassembly. Remove cotter pin, then loosen the nut, but leave on by a few threads. Them take a hammer and hit the spindle housing where the ball joint goes through. After a few whacks, the arm should pop up and you can finish removing nut. Once you have the upper arm lose, you can see the top shock bolt/nut. There is a special tool that makes this removal easier, but an open end wrench and vise grips can work also. I ended up using a 4 ½” angle grinder with a metal cutoff blade and cut the nut/bolt off. Just be careful not to cut into the arm or frame area. Once you get that lose, you can remove the lower bolts form the lower arm, 13mm socket will do the trick. Once that is lose, you can wiggle the shock down and out. Keep the lower bolts; you will need for new shocks.
5. Now the stabilizer bar needs disconnected. This will take a wrench and socket. All that needs to be done is the nut removed and the bushings taken off. This will allow the bar to be free. This would also be a good time to install need links while our in there if so desired.
6. Next, the old stock spring will need to come out. Since the upper arm is already apart, this is just a matter of pushing the lower control arm and spindle/brake rotor down and getting spring out. This may take some persuasion with a crowbar, mine actually came out fairly easy. Once this is out, you can clean all the dirt buildup from the spring pockets. Now on to the most fun part……
7. Install of new lift springs…these are some bad boys!!!! I Express EXTREME CAUTION at this step, these springs need to be compressed and are very dangerous. These springs have to compressed some to get them in. I rented and inside spring compressor from Autozone and compressed my springs with an air hammer. Be very careful with these as there is a lot of compressed energy just waiting to get lose and hurt someone. Once these are compressed they can be installed into the spring pockets. There is only one way to install, the flat goes to the top, the open coil goes on bottom with the end of the coil being placed between the two small holes in the spring pocket, this gives proper alignment. The stock springs came with a rubber isolator on top, I tried to re-install, but they wouldn’t stay on so I left them off, no problems since. This was the worst step of the entire lift to try to get spring in the pocket and back in. I ended up placing a small jack under the control arm and putting some pressure on it while trying to pry spring into the pocket. This took some finesse and a lot of prying and jacking, I still don’t know I got them in, but I did. The last one actually had the spring compressor let lose just as it slipped into place…..That’s what I meant by extreme caution, I could have had a broken leg or something if it would have come out instead of in. I would recommend having a professional install these for you if you have any reservations about this step. Once they are in and seated, you can begin putting everything back together in reverse order. I also recommend before reconnecting the upper arm, remove the upper rubber bump stop from the arm and cut it down some. I used two screwdrivers to pry it out from the top and then took it to the bench and used a cut off tool in my angle grinder cut approx ½- ¾” off of it. Cutting of the bump stop allows the top control arm to come down enough to get ball joint back into hole and re-attached. Then I replaced and continued with replacement of all parts in reverse order; upper control arm/ball joint, stabilizer bar, brakes, ABS cable, shocks, and then tires. Make sure everything is tight and steering works correctly.
Installation of 2” rear axle blocks, rear add a leaf, and shocks:
1. As in the other steps, make sure vehicle is in park and front wheels blocked. Jack up rear of van, remove rear tires, and place jack stand under rear frame right in front of rear springs. I left jack under differential and placed another jack stand under my trailer receiver for extra safety (if you have one).
2. Begin by removing the rear shocks, saving both the top and lower bolts and nuts as they will be re-used on the new shocks; discard old shocks will be needed with lift.
3. Now begin removing Ubolts and bolt/nut assemblies that hold axle to leaf springs. The jack under the axle will be need to lower the axle once lose from springs. Once the bolts are off, you can then lower axle and proceed to either placement of either axle block or extra leaf.
A. The rear axle lift block can be purchased at your local auto shop or through Overlands. I used a 2” block and had to get new ½” Ubolts as the supplied ones were too long for my astro. Once the old Ubolts are lose, you can lower jack and separate the axle from springs. I removed the rubber pad and placed the new block in between the axle and springs. The center hole may need enlarged slightly to fit over the leaf spring center pin. Once in place, raise jack and get axle/block back in place. Then the new Ubolts can be put in place and finger tighten on top plate. The inner bolts will need replaced as they will now be too short. Place the lower bracket on a work bench or place in vise and pound out the old bolts. The are tack welded in place so some force may be required. Once they are out, replace with some new grade 8, 3” bolts. I also bought some ½” black iron pipe and cut to 2” to use as a spacer between the upper and lower brackets. Once you get all the assembly together, you can then tighten all bolts to specs (I just torqued everything down pretty tight).
B. The other choice is using Overland’s add a leaf (use their instructions if included) which also requires the Ubolt/inner bolts to be remove and the axle to be separated from axle. The spring retaining clamps on each end must then be bend open so springs can be separated; this can be done with crowbar/large pry bar. After that is done, the center pin can be removed to allow the separation of springs either by unbolting or using cut off tool. Place a large C clamp on spring near center to prevent spring from flying apart once center pin is removed. Slowly remove clamp to allow springs to separate. Now place the add a leaf spring in its proper place (follow Overlands instruction). NOTE: I used a leaf spring out of a K5 blazer as my add a leaf. I had to cut the ends down some and it was just slightly wider, but worked fine and I placed it directly under the top spring. This gave me about an inch extra lift and slightly more carrying capacity.
Once you get your leaf in place, use the c clamp to compress the pac so you can put the new longer center pin back in. Once that is in and tight, replace the Ubolts/inner bolts and bracket and tighten everything back up. You then will need a large c clamp (6”) to squeeze the spring retaining clips back together.
4. Now that you have either your blocks in or leafs, the new shocks can be installed. I chose the recommended Rancho shocks form Overlands’ website. There will be supplied steel bushing which need to be place inside the poly bushings in the shocks. You can then replaced the factory bolts/nuts and tighten. These need to be fairly tight or you will get a banging noise when hitting bumps, but not too tight as to crush the poly bushing. If you do get a banging after install, just retighten nuts. Replace the wheels and you should be ready to go.
Hopefully, these instructions will cover the complete install of the lift kit on a rear wheel drive astro/safari.
Remember after install it is important to have van properly aligned at a tires store. I had problems with too much positive camber and my alignment guy recommended I order some offset upper control arm inner shafts to correct. He stated he could place shims in there to get proper alignment, but he was afraid that it would make van too unsafe to drive. As of this writing, shafts are ordered and will be installed. I also recommend after a week or two of driving to go back over every nut/bolt and check tightness as things may work lose as they settle in.
09/20/06: UPDATE, upper offset control arm shafts were installed and alignment was set perfect, they were definitely the trick I needed.
Marty Sackenheim
“BLAZER”
Contact at;
http://www.astrosafari.animegrafx.com
blazercdr@yahoo.com
2wd Astro w/5" Lift
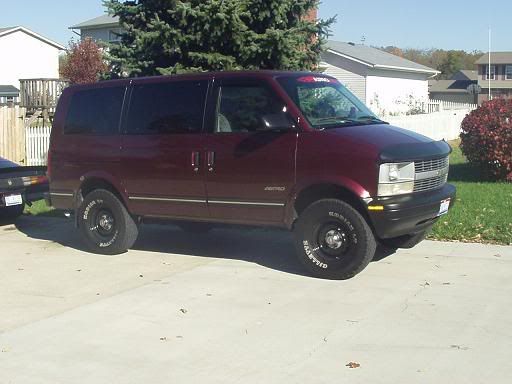
Front body Lift
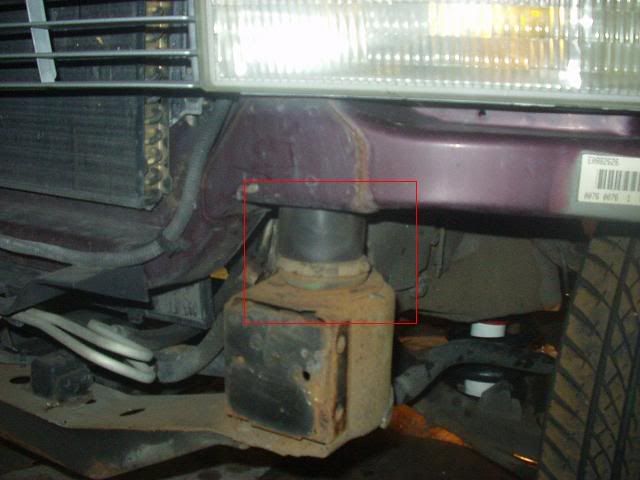
Rear Shackles
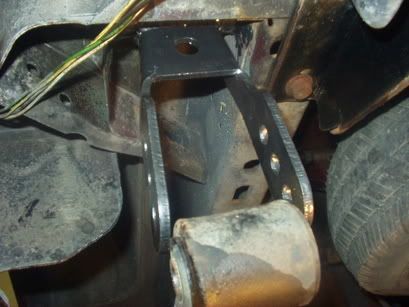
Coils (new and old)
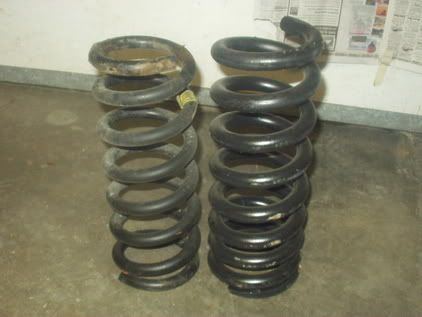